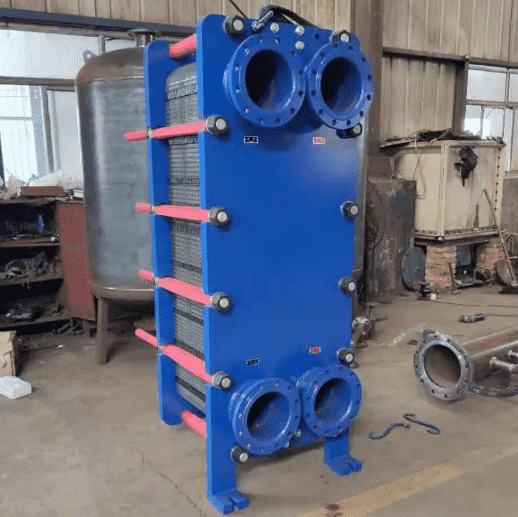
Plate Fin Heat Exchanger
Our aluminum plate fin heat exchangers (PFHEs) are key components in many process plants. Their compact footprint helps save space and costs in a wide range of facilities, including air separation plants, petrochemical and gas treatment plants as well as natural gas and helium liquefaction plants.
Our heat exchangers composes of corrugated fin and separation plate which are stacked and brazed. Comparing to the other type of heat exchangers, by enlarged heat transfer area , this type of heat exchanger becomes more compact and lighter. We can produce from large to small heat exchanger, and take flexible material choices, such as aluminum alloy, and stainless steel etc.
Aluminum units can be made up to 1.2 m × 1.2 m cross section and 6.2 m long.
Stainless steel units can be made up to 500 mm × 500 mm cross section × 1500 mm length.
There are two important subclasses of plate-fin heat exchangers, namely, the plate-fin-plate-fin construction and the plate-fin-tube construction. The plate-fin-plate-fin construction, which consists of a number of laminations of the elements in Figure 1, is normally used for gas-to-gas (or two-phase) applications. The plate-fin-tube construction, which has tubes normal to the plate structure, is used for gas-to-liquid or gas change of phase applications; the liquid or two-phase mixture flows through the tubes. The passenger car radiator and air-conditioning condenser are examples of this construction.
The most common construction material is all aluminum, which yields what are called “brazed aluminum heat exchangers.” These have an extremely wide variation in core size-from the gargantuan sizes used in industrial gas processing to quite small sizes used in automotive applications (e.g., a heater cores) or aircraft (e.g., oil coolers).